Forged for One
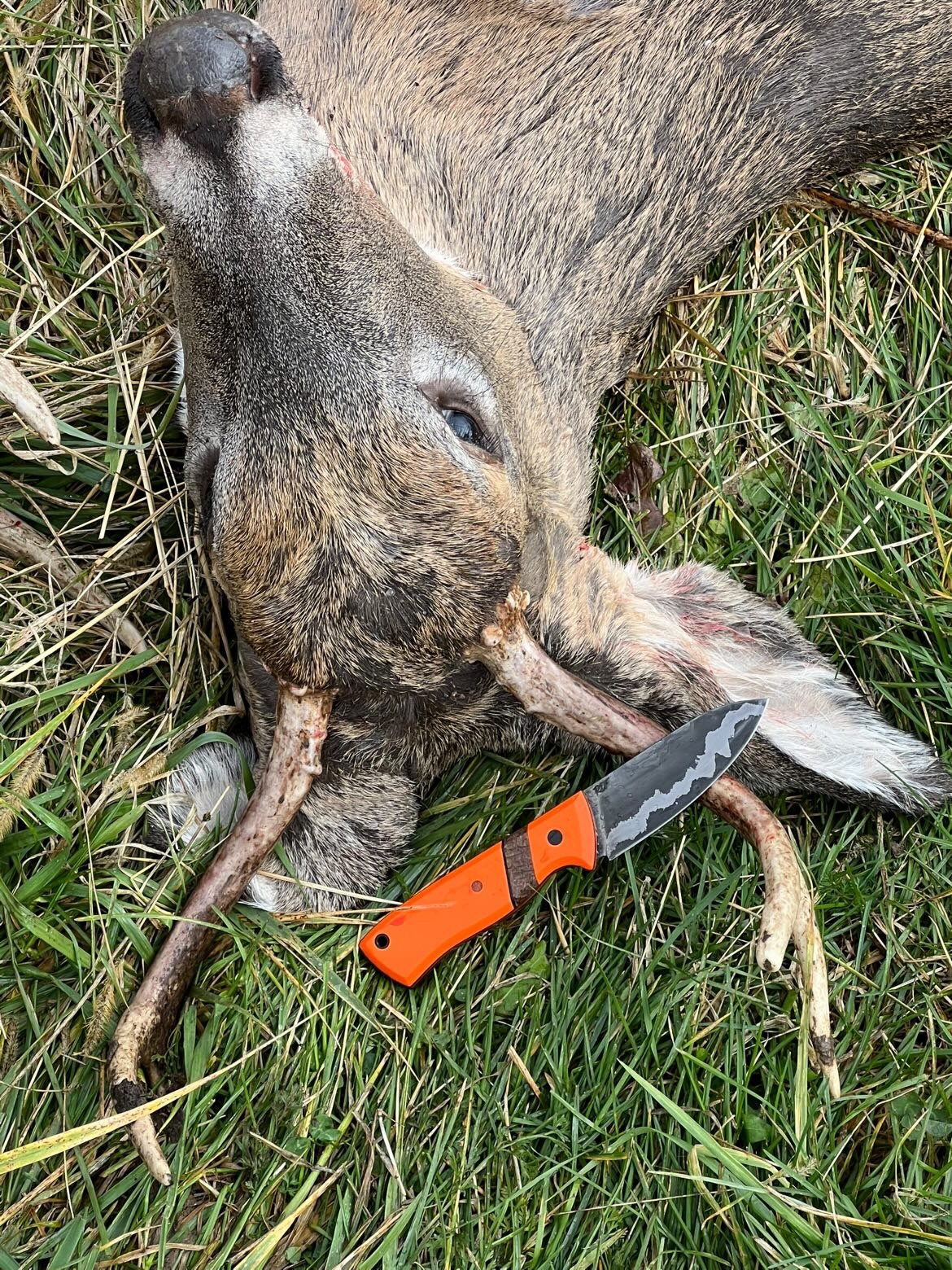
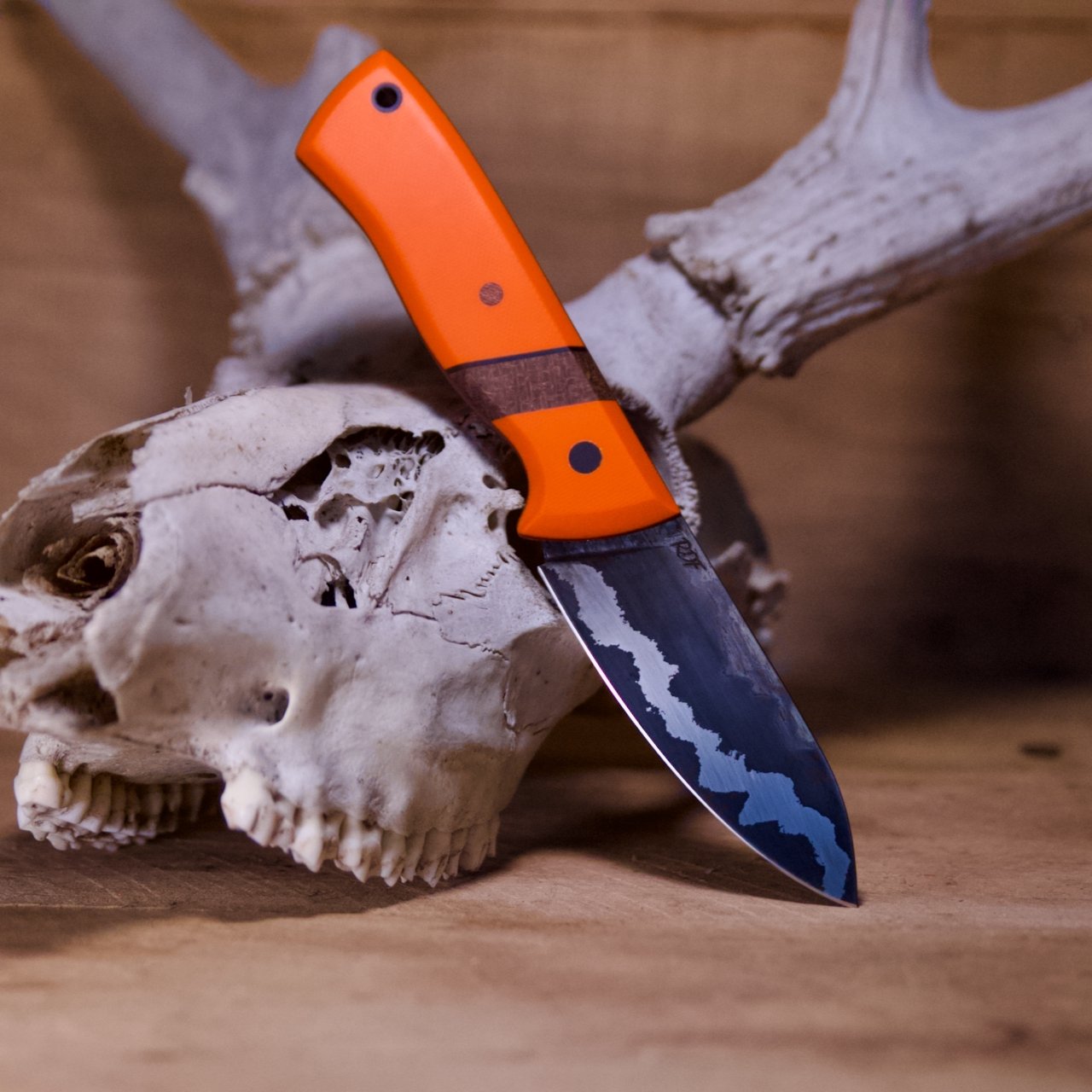
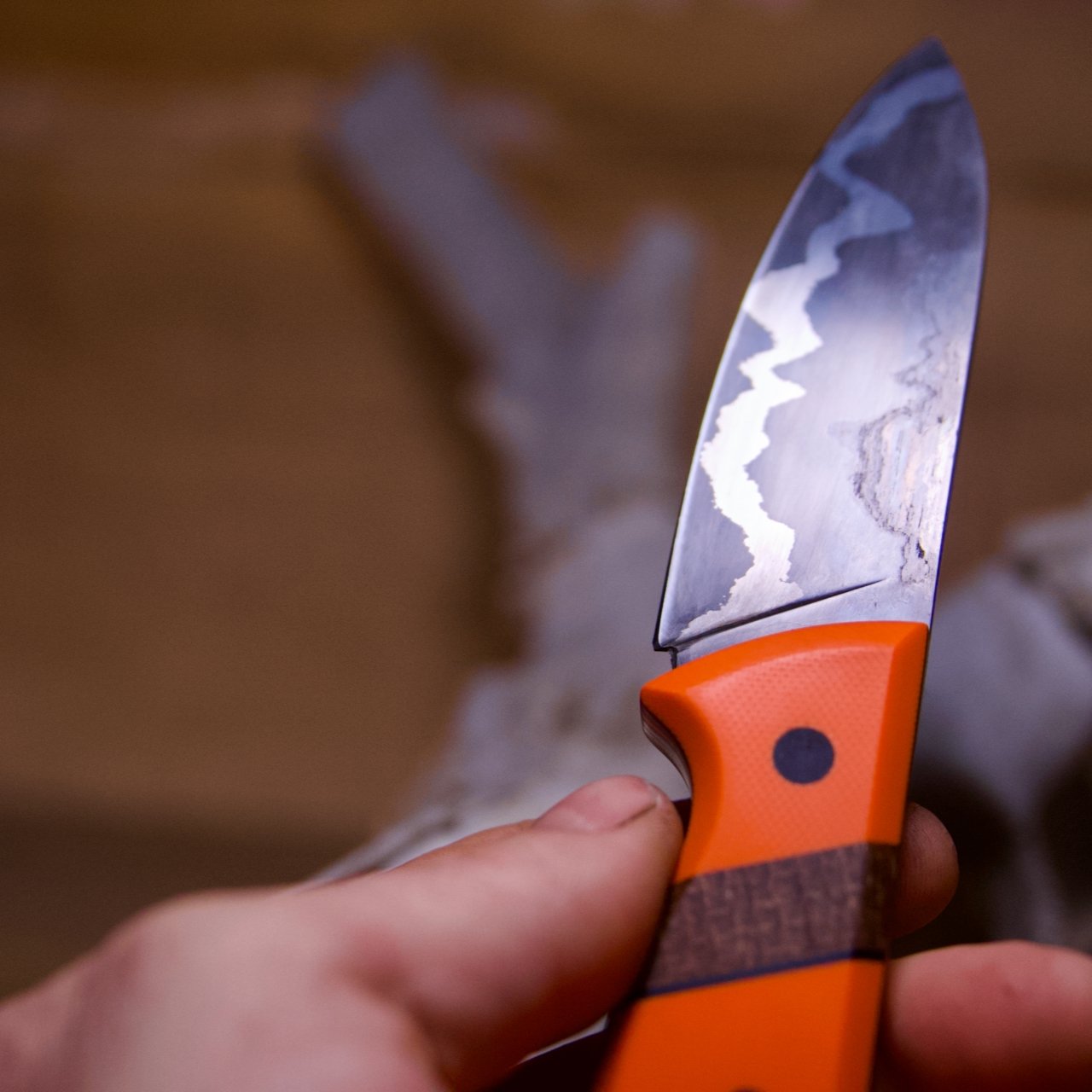
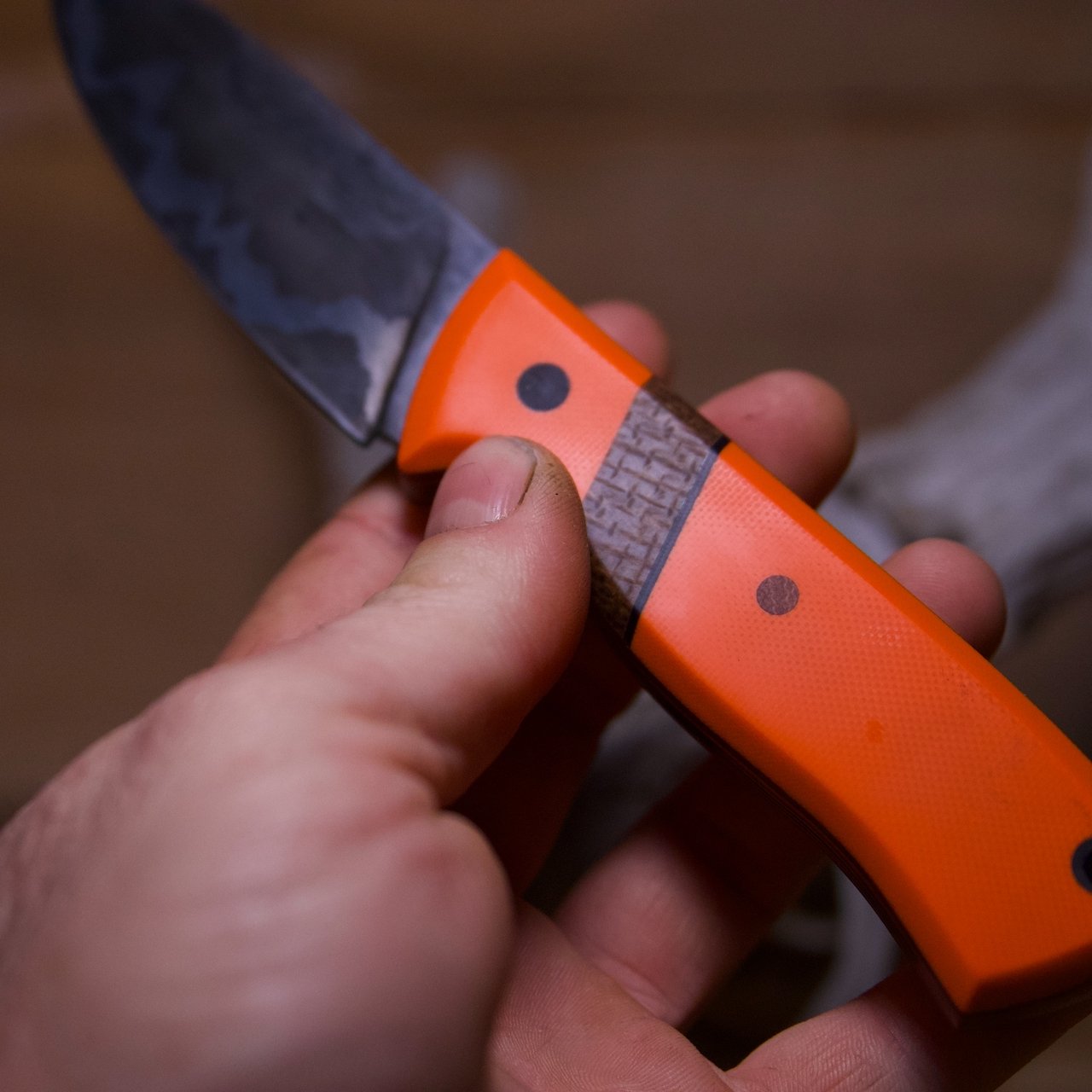
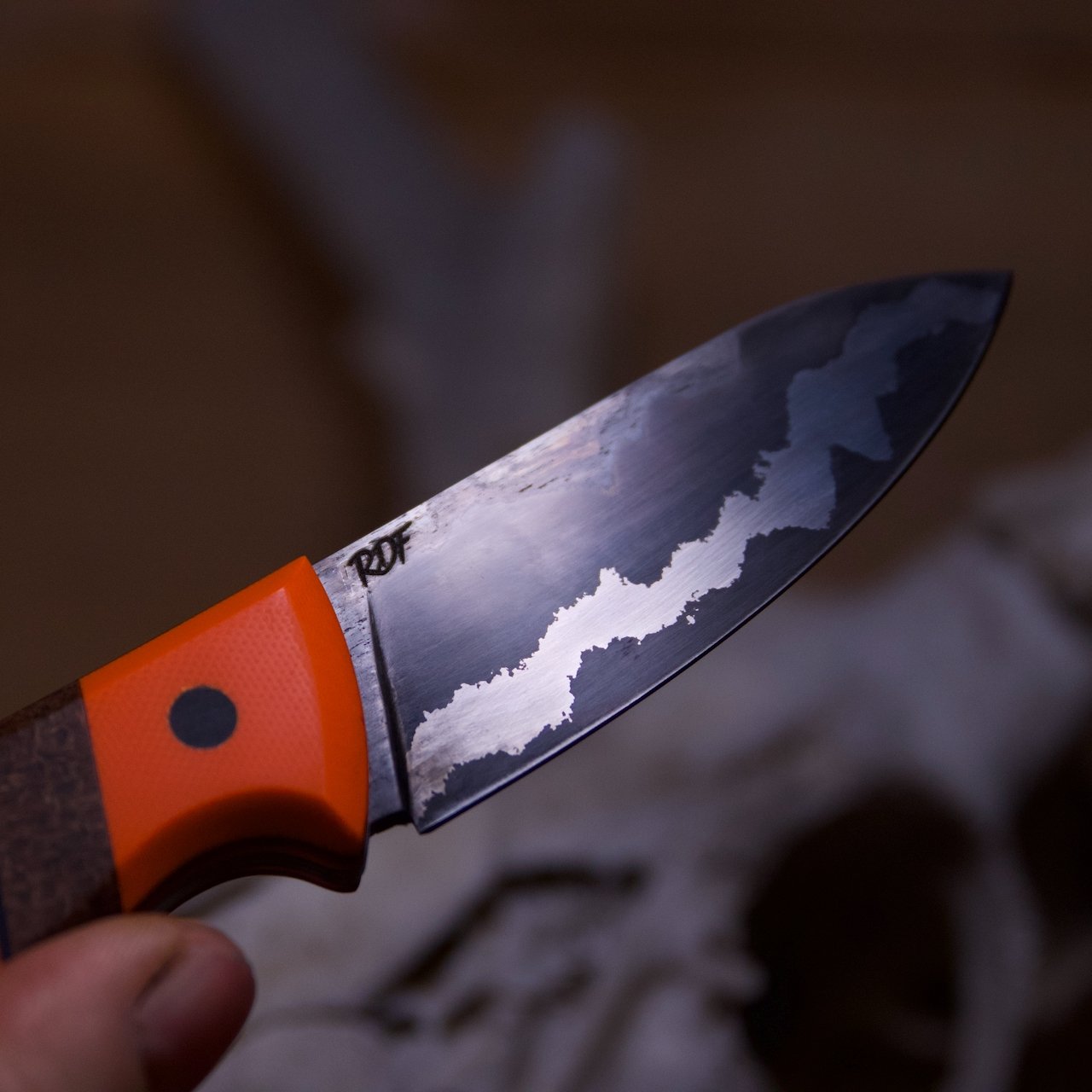
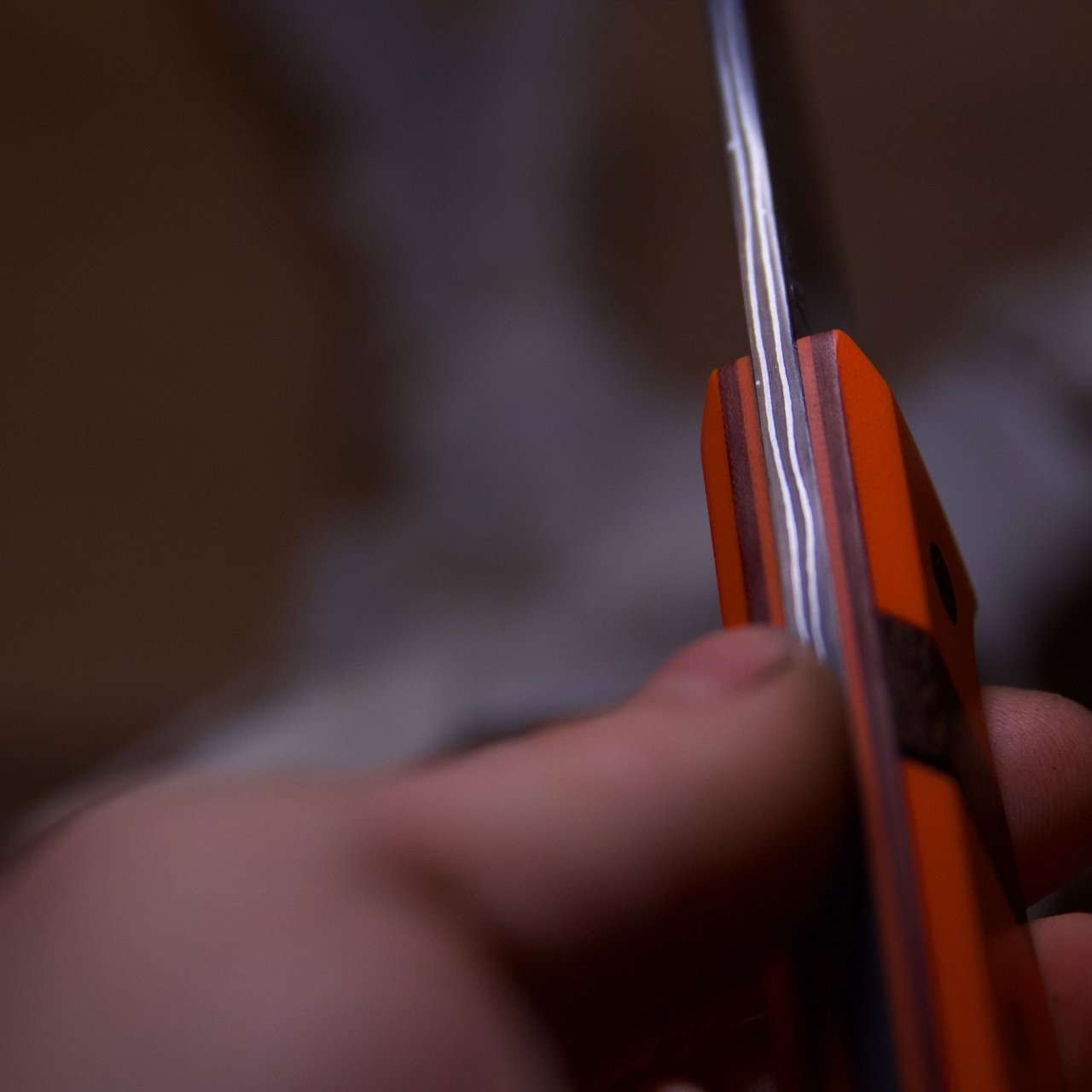
Every custom knife I make is a collaboration. The customer brings a vision—something personal, something that stands apart from the basic, off-the-shelf blades. My job is to bring that vision to life, no matter how many tries it takes.
This knife? It took four billets to get it right.
Forge-welding layered steel is no joke. When you quench the billet, each metal contracts at a different rate. If you’re not careful, you end up with delaminations or cracks—especially when using a jacketed design. For this build, I used a wrought iron jacket and a high-carbon steel core. Problem is, wrought iron doesn’t contract as much as the core steel. That mismatch? It cracked the blade. Three times.
What finally worked was switching the core material to 1084. That gave me the stability I needed without compromising performance.
And the handle—hunter orange G10 with a black liner, burlap micarta, and pinned construction—hits the mark. Unique, bold, and made to be used.
Mike sent me a photo of his knife in the field, doing real work. That’s why I do this. Because when someone asks for a knife that stands out—I make sure they get it.